Изготовление литейных форм и стержней: технология производства и материаловедение
Литейное производство является одним из ключевых этапов в цепочке создания металлических изделий и конструкций. Этот процесс требует высокой точности, ведь от качества литейных форм и стержней зависит итоговое качество готового продукта.
В данной статье мы подробно рассмотрим материалы и технологии, используемые в производстве литейных форм и стержней, а также основные этапы и особенности их изготовления.
Содержание:
Какие материалы используются для изготовления литейных форм и стержней?
Технологический процесс литья под давлением и его особенности
Основные этапы изготовления литейных форм: от модели до отливки
#Какие материалы используются для изготовления литейных форм и стержней?
#Основные типы смол и их роль в литейном производстве
В литейном производстве смолы играют важнейшую роль в качестве связующего компонента формовочных смесей. Зачастую используются фенольные, фурановые и силикатные смолы, каждая из которых обладает уникальными характеристиками уплотнения и твёрдости. Эти компоненты придают литейной форме необходимую механическую прочность и улучшают точность готовых отливок.
Смолы, используемые в литейном производстве, действительно играют критически важную роль, обеспечивая создание качественных и точных литейных форм и моделей. В зависимости от конкретных требований к отливке и литейной форме, применяют различные типы смол.
Давайте подробнее рассмотрим характеристики основных видов смол, используемых в литейной индустрии:
Фенольные смолы - имеют высокую механическую прочность и хорошую термическую стойкость, что делает их подходящими для производства тяжелых литейных форм и сердечников, применяемых при литье под высоким давлением и при высоких температурах. Фенольные смолы также обладают хорошей стойкостью к воде и химикатам, что может быть критично для некоторых применений.
Фурановые смолы - обладают высокой термической стабильностью и прочностью, что делает их идеальными для создания литейных форм для чугуна, стали и цветных металлов. Фурановые смолы характеризуются высокой стойкостью к износу и могут выдерживать экстремальные температуры, что делает их предпочтительным выбором для сложных отливок.
Силикатные смолы - применяются в сочетании с другими веществами для создания силикатных связующих систем. Они имеют хорошую адгезию и обеспечивают прекрасную стабильность формы при высоких температурах. Силикатные смолы экологически безопасны и обладают низким уровнем токсичности, что делает их подходящими для использования в условиях, где необходимо соблюдение строгих экологических стандартов. Благодаря своей способности выдерживать высокие температуры без значительного разложения, силикатные смолы используются для изготовления форм и сердечников, которые могут подвергаться воздействию экстремального тепла во время процесса литья. Это делает их идеальным выбором для отливок из цветных металлов и сплавов с высокой точностью деталей.
Каждый из этих типов смол выбирается в зависимости от конкретных требований к отливке, включая температуру плавления металла, требуемую прочность и точность отливки, а также влияние на окружающую среду. Выбор подходящего типа смолы позволяет оптимизировать процесс литья, обеспечивая высокое качество готового продукта и эффективность производственного процесса.
Использование современных смол в литейном производстве не только повышает качество и точность литейных изделий, но также способствует повышению производительности за счет сокращения времени на подготовку и обработку форм и сердечников. Кроме того, применение экологически безопасных и малотоксичных смол способствует снижению воздействия производственного процесса на окружающую среду, что является важным аспектом в условиях возрастающей экологической осведомленности и требований.
#Преимущества и недостатки использования кварцевого песка в литейном деле
Кварцевый песок является традиционным и наиболее распространённым материалом для создания литейных форм благодаря своей доступности, теплоустойчивости и пластичности. Однако, несмотря на многочисленные преимущества, использование кварцевого песка связано с риском образования дефектов на поверхности отливок, что требует тщательного контроля качества формовочной смеси.
#Технологический процесс литья под давлением и его особенности
#Этапы подготовки и заливки металла в форму под давлением
Литьё под давлением предполагает заполнение металлом литейной формы под высоким давлением. Этапы подготовки включают подготовку и нагрев металла до жидкого состояния, заливку его в форму и охлаждение до затвердевания.
Использование под давлением позволяет достигать высокой плотности и точности деталей, минимизируя пористость и другие дефекты. Литьё под давлением является сложным и высокотехнологичным процессом, который требует тщательной подготовки и контроля на каждом этапе производства детали.
В общих чертах, процесс можно разделить на несколько основных шагов:
Подготовка литейной машины и формы
- Очистка формы: Удаление остатков материала и загрязнений с предыдущих циклов заливки.
- Смазка формы: Нанесение тонкого слоя смазки для облегчения извлечения отлитых изделий и защиты формы.
- Установка формы на литейную машину: Подготовка и закрепление формы, проверка её герметичности.Подготовка металла
- Выбор металлического сплава: В зависимости от требований к изделию подбирается конкретный сплав.
- Плавление металла: Металл загружается в специальную печь, где он плавится до нужной температуры.Заливка металла в форму
- Нагнетание металла под давлением: Жидкий металл под большой скоростью и давлением вводится в полости формы. Давление поддерживается до полного затвердевания металла.
- Управление давлением и скоростью заливки: Оптимизация параметров давления и скорости заливки для достижения лучшего качества изделия.Охлаждение и затвердевание
Охлаждение в форме: Форма остается закрытой, пока металл затвердевает. Время охлаждения может варьироваться в зависимости от размера и сложности изделия.
Выемка изделия: После достаточного охлажд ения и затвердевания металла форма открывается, и готовое изделие извлекается. Этот процесс может потребовать использования специальных механизмов или роботов для минимизации риска повреждения изделия и формы.Послеобработка
Очистка и обрезка: Удаление лишних элементов, образовавшихся в процессе литья, таких как литниковые системы и подпорки. Это может включать резку, шлифовку или обработку давлением.
Термическая обработка: Для повышения прочности и улучшения механических свойств изделия может быть проведена термическая обработка, такая как отжиг, закалка или старение.
Поверхностная обработка: Для улучшения внешнего вида, устойчивости к коррозии или улучшения свойств поверхности изделия могут быть применены различные виды покрытий или пассивации.
6. Контроль качества
Визуальный осмотр: Проверка внешнего вида и отсутствия видимых дефектов на поверхности изделия.
Измерение и тестирование: Использование различных инструментов и методов для проверки размеров, твердости, прочности на разрыв и других характеристик изделия.
X-ray или ультразвуковой контроль: Для выявления внутренних дефектов, таких как поры или недоливы, которые могут повлиять на прочность и долговечность изделия.
Литьё под давлением требует высокого уровня точности и контроля над процессом, чтобы обеспечить производство качественных изделий. Современные литейные машины и технологии позволяют автоматизировать многие аспекты процесса, улучшая его эффективность и снижая вероятность возникновения ошибок. От точности подготовки и соблюдения технологического процесса зависят не только качество и свойства получаемых изделий, но и экономическая эффективность производства.
#Как достигается высокая точность деталей при литье под давлением
Высокая точность литых деталей достигается контролем температуры металла и давления в процессе заливки и затвердевания. Специальное оборудование позволяет точно регулировать эти параметры, обеспечивая однородность заполнения формы и минимизацию дефектов.
#Различия между литьем под давлением и традиционным литьем
Главное отличие литья под давлением от традиционного состоит в использовании высокого давления для заливки металла в форму, что обеспечивает более высокую прочность и точность деталей. Традиционное литьё, в свою очередь, часто применяется для крупных отливок или когда высокая точность не является приоритетом.
#Основные этапы изготовления литейных форм: от модели до отливки
#Как создается модель будущего изделия
Модель для литейной формы создается на основе чертежей будущего изделия, часто с использованием 3D-моделирования. Эти модели могут быть выполнены из различных материалов, включая пластик, дерево или металл, и служат основой для создания рабочих форм для отливки металл Создание модели будущего изделия для литейной формы в современном производстве проходит несколько ключевых этапов, включающих как компьютерное моделирование, так и реальное производство модели.
Подробно рассмотрим эти процессы:
Разработка концепции и проектирование. Перед созданием физической модели разрабатывается концепция будущего продукта. На этом этапе проводятся исследования, анализ возможных конструкций, функционалов и спецификаций продукта. Затем на основе этих данных создается электронная 3D-модель изделия с использованием САПР (системы автоматизированного проектирования), таких как SolidWorks, AutoCAD, CATIA и т.д.
3D-моделирование. С помощью САПР-программ инженеры создают подробные 3D-модели изделия, учитывая все технические детали, такие как размеры, формы, толщину стенок и расположение элементов. Эти модели позволяют визуализировать изделие до его физического создания, провести анализ прочности, усталости, динамики и других параметров.
Выбор материала для модели. Материал для создания модели выбирается в зависимости от технологии изготовления формы и параметров будущего литья. Для прототипов часто используют пластик, полиуретан, дерево, воск или металл. Выбор материала обусловлен необходимостью точного воспроизведения деталей модели, а также экономическими и технологическими соображениями.
Прототипирование. Для изготовления прототипа могут использоваться различные методы, включая 3D-печать, литье под аналогичное давление, фрезерование или стереолитографию. Прототипирование позволяет получить физическое воплощение 3D-модели, которое можно оценить "в руках", проверить на соответствие проектным требованиям, а также использовать для демонстрации заказчикам или для тестирования в реальных условиях эксплуатации. Этот этап критичен для выявления потенциальных проблем дизайна или производства до начала массового производства.
Создание рабочей модели. После аппробации прототипа и внесения необходимых корректировок создается рабочая модель, которая будет использоваться для изготовления литейной формы. В зависимости от выбранного метода литья, модель может быть выполнена из материала, который легко удаляется из формы после заливки металла (например, вос при литье по выплавляемым моделям) или из материала, обладающего достаточной прочностью для создания формы методом обратного литья.
Изготовление литейной формы. На основе рабочей модели создается литейная форма. Это может быть выполнено разными способами, включая механическую обработку (например, фрезерование) для создания формы из твердых материалов, таких как сталь или алюминий, или использование рабочей модели для литья формы из силикона или других гибких материалов в случае литья под давлением малых партий.
Тестирование формы и корректировка. Перед началом серийного производства проводится тестирование формы для выявления возможных дефектов отливки и определения необходимости доработки дизайна формы или процесса литья. Этот шаг позволяет убедиться, что конечный продукт будет соответствовать всем требованиям и стандартам качества.
Запуск серийного производства. После всех проверок и корректировок литейная форма готова к использованию в серийном производстве. Процесс литья может быть автоматизирован для обеспечения высокой производительности и постоянства качества продукции.
Каждый из этих этапов требует высокой квалификации специалистов и использования передовых технологий, что позволяет сократить время и затраты на разработку новых продуктов, а также гарантировать их высокое качество и соответствие требованиям заказчиков.
#Способы формирования полости формы для последующего заливания металла
Для формирования полости в литейной форме могут использоваться различные методы, включая моделирование по выплавляемым моделям и механическую обработку. Выбор метода зависит от требуемой точности, характеристик материала и сложности изделия.
#Контроль качества литейной формы перед началом отливки
Перед началом процесса отливки проводится тщательный контроль качества литейной формы, который включает проверку чистоты и отсутствия дефектов поверхности, проверку точности геометрии и соответствия размеров. Это обеспечивает получение высококачественных отливок и снижение доли брака.
#Процедуры подготовки и использования стержней в литье
#Типы стержней и их назначение в литейных формах
Стержни используются в литейных формах для формирования внутренних полостей и каналов в отливке. Они могут быть выполнены из песка, металла или других материалов в зависимости от требований к отливке. Ключевым аспектом является их способность выдерживать высокие температуры без деформации.
#Методы уплотнения и расположения стержней в форме
Для обеспечения точности и прочности внутренних каналов отливки стержни должны быть правильно уплотнены и расположены внутри формы. Это требует точного расчета их положения и использования специальных крепежных элементов для поддержания стержней на месте во время заливки металла.
#Особенности сушки и обработки стержневых оснасток
После расположения в форме, стержни подвергаются процессу сушки, что улучшает их прочностные характеристики и предотвращает деформацию во время заливки металла. Обработка стержневых оснасток может также включать покрытие специальными защитными составами для предотвращения прилипания металла.
#Применение оболочковых форм в литейном производстве
#Что такое оболочковые формы и в чем их преимущества
Оболочковые формы представляют собой тонкие, но прочные формы, изготавливаемые с использованием оболочковых смол и песка. Основным преимуществом является возможность получения гладких и точных поверхностей отливок, а также значительное снижение веса формы, что упрощает обращение с ней.
#Как изготавливаются оболочковые формы и чем они отличаются от песчаных
Изготовление оболочковых форм включает нанесение смолы на модель, обсыпку песком и термообработку. В отличие от традиционных песчаных форм, оболочковые формы требуют меньше материала для их создания, обеспечивая при этом высокое качество поверхности отливок.
#Технологические нюансы литья в оболочковые формы
Литьё в оболочковые формы требует определённых технологических нюансов, таких как точный контроль температуры и давления. Это позволяет максимально использовать преимущества формы для достижения высокой детализации и качества поверхности готовых отливок.
#3D-печать литейных форм
#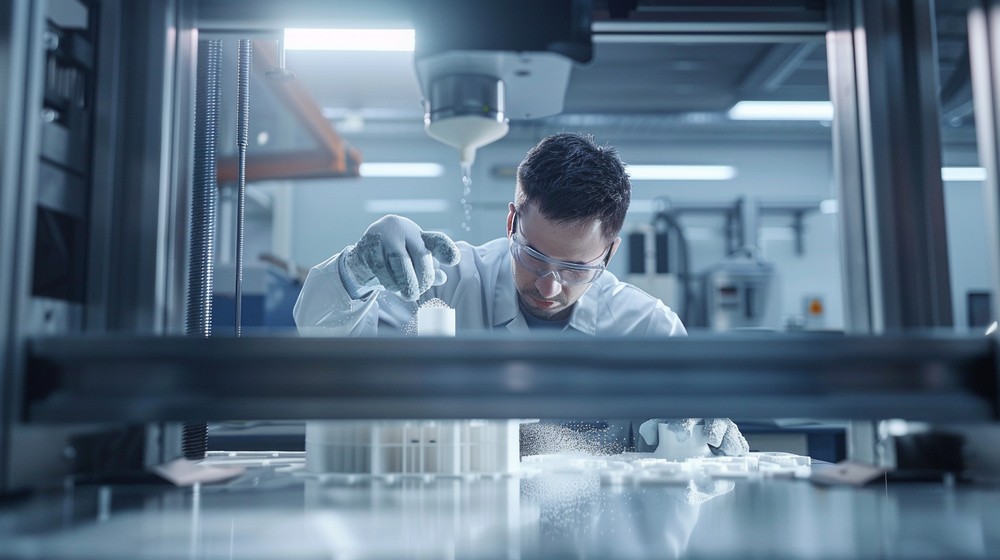
3D-печать литейных форм – это революционный метод в производстве, который значительно ускоряет и упрощает процесс создания сложных деталей и конструкций.
Этот метод позволяет производить литейные формы для последующего отлива из различных материалов (металлов, пластмассы, силикона, и т.д.) с высокой степенью точности и сложности конфигурации, которые трудно или невозможно изготовить традиционными способами.
Процесс 3D-печати литейных форм может использовать различные технологии, включая SLS (Selective Laser Sintering, селективное лазерное спекание), SLA (Stereolithography, стереолитография), FDM (Fused Deposition Modeling, моделирование методом наложения расплавленного материала) и другие. Выбор технологии зависит от требуемых характеристик, таких как размер, сложность и тип материала изготавливаемой детали.
Преимущества 3D-печати литейных форм:
Сокращение времени производства. Создание литейных форм с помощью 3D печати значительно сокращает время, необходимое для их производства, по сравнению с традиционными методами, включая фрезерование или токарную обработку.
Сложность конструкции. 3D-печать позволяет проектировать и изготавливать формы с высокой степенью сложности, которые были бы невозможны или чрезвычайно затратны при использовании других методов.
Прототипирование. Благодаря своей гибкости и скорости, 3D-печать литейных форм идеально подходит для быстрого прототипирования, позволяя производителям тестировать различные дизайны перед финальным производством. Это не только сокращает общее время разработки продукта, но и позволяет оптимизировать конструкцию для улучшения её качества и функциональности.
Снижение стоимости. Использование 3D-печати для создания литейных форм может значительно снизить стоимость производства за счёт уменьшения необходимости вручную изготавливать сложные формы и сокращения количества отходов материала. Также уменьшаются затраты на исправление ошибок, поскольку изменения в дизайне могут быть легко внесены в цифровую модель.
Устойчивость и экологичность. 3D-печать способствует более устойчивому и экологически чистому производству. Поскольку этот метод позволяет точно использовать необходимое количество материала для создания формы, значительно уменьшается объем отходов. Кроме того, возможность локального производства сокращает необходимость в транспортировке, что дополнительно уменьшает углеродный след производства.
Персонализация продукции. 3D-печать позволяет легко адаптировать литейные формы под конкретные нужды заказчика, что открывает широкие возможности для персонализации продуктов. Это особенно важно в таких областях, как медицина, зубопротезирование и ювелирное дело, где требуются уникальные, подходящие именно под конкретного пользователя изделия.
Повышение качества продукции. Точность и возможности кастомизации, которые предоставляет 3D-печать, способствуют повышению качества готовых изделий. Улучшенная точность формы позволяет получать изделия с лучшей поверхностной отделкой и детализацией, что особенно важно для сложных или высокоточных компонентов.
#Технология Binder Jet для производства литейных форм
Технология Binder Jet (процесс печати с использованием связующего) представляет собой метод 3D-печати, где основным принципом является поэтапное распыление жидкого связующего по слоям порошкового материала, например, металлического порошка, песка или керамического материала. После процесса печати полученный объект проходит дополнительную термическую обработку, если это необходимо, для достижения окончательной прочности и функциональных характеристик. Binder Jet технология находит широкое применение в различных областях, включая производство литейных форм, что является одним из её ключевых направлений использования.
В контексте создания литейных форм для отливки металлических изделий, технология Binder Jet предлагает несколько значительных преимуществ:
Быстрое изготовление. В отличие от традиционных методов изготовления литейных форм, таких как моделирование из песка и мастичные формы, Binder Jet позволяет быстро создавать сложные формы без необходимости изготовления физических моделей или специализированных инструментов.
Сложность конструкций. Технология позволяет реализовывать сложные детали с высокой точностью и детализацией, включая создание внутренних каналов и пустот без значительного увеличения стоимости производства.
Экономия материалов и сокращение отходов. Поскольку материал используется только там, где это необходимо для создания части формы, технология позволяет сократить количество отходов и, как следствие, снизить расходы на материалы.
Сокращение времени на изготовление и сборку. Применение технологии Binder Jet в производстве литейных форм позволяет существенно сократить время, необходимое для подготовки и выполнения заказа, поскольку устраняется необходимость в ручной работе и использовании сложного оборудования. Это особенно важно при производстве мелких партий или при необходимости быстрого внесения изменений в конструкцию изделий.
Улучшенные свойства отливок. Использование литейных форм, созданных с помощью технологии Binder Jet, может улучшить качество отливок за счет более точного контроля над процессом формирования и охлаждения отливаемого металла. Это позволяет получать изделия с более высокой механической прочностью и уменьшенным количеством дефектов.
Возможность использования различных материалов. Технология позволяет использовать широкий спектр порошковых материалов, включая специализированные типы песка и металлические порошки, что дает возможность изготавливать литейные формы для широкого круга отливаемых материалов.
Экологичность. Производство литейных форм с помощью технологии Binder Jet является более экологичным вариантом по сравнению с традиционными методами, так как оно позволяет сократить энергопотребление и количество отходов.